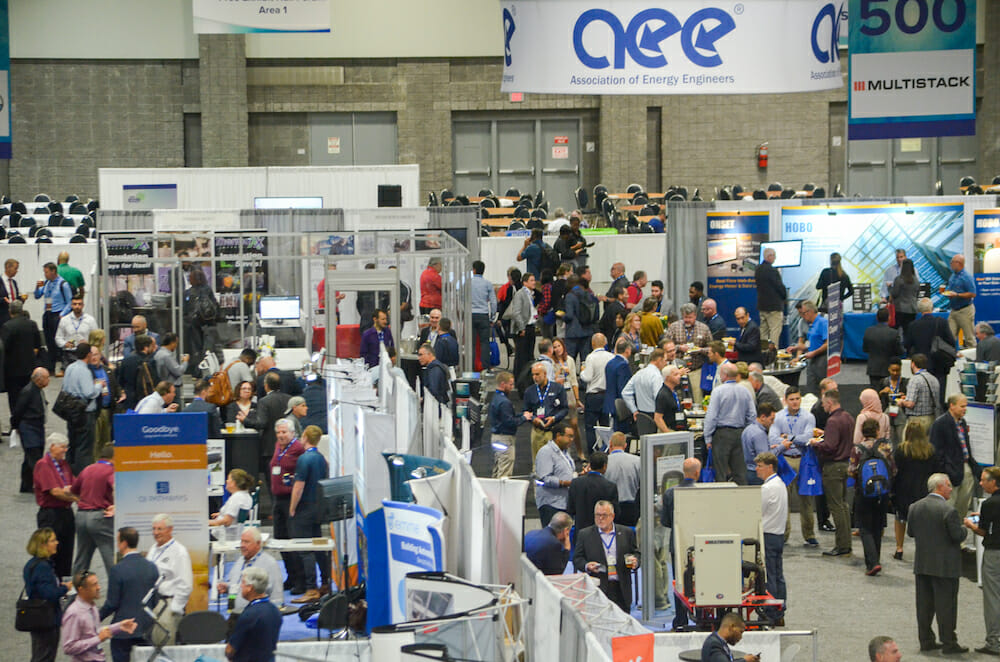
Introducing Tagup Inc.
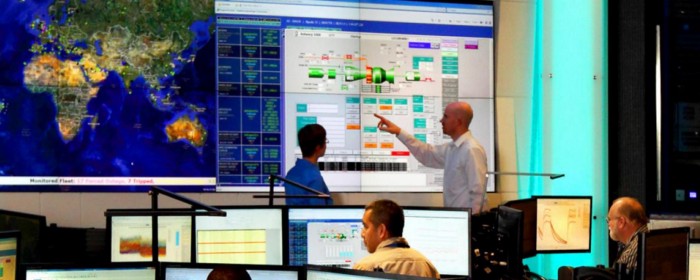
We are excited to announce Tagup, our new company building a platform to consolidate industrial equipment data and predict/diagnose equipment failure.
A brief history
Companies like Rolls Royce, Siemens, and GE can remotely monitor very large assets around the world, including jet engines and steam turbines. These multimillion dollar assets are critical to operations in aviation, power generation, and water.
With tens or even hundreds of subject matter experts reviewing the data, these companies can provide recommendations and support to their end customers, ensuring their equipment remains in service and in good health.
When I worked at GE, I always wondered: why isn’t this service available for any equipment type? Why only for the most critical assets, often priced well over $10 million?
The answer: cost. It is expensive to set up a remote monitoring center, to instrument the equipment in the field, to staff the fifty or more engineering subject matter experts, and to provide the support required to end customers. The cost of equipment failure, both in terms of business interruption and equipment breakdown, must be enormous to justify the high average fixed cost
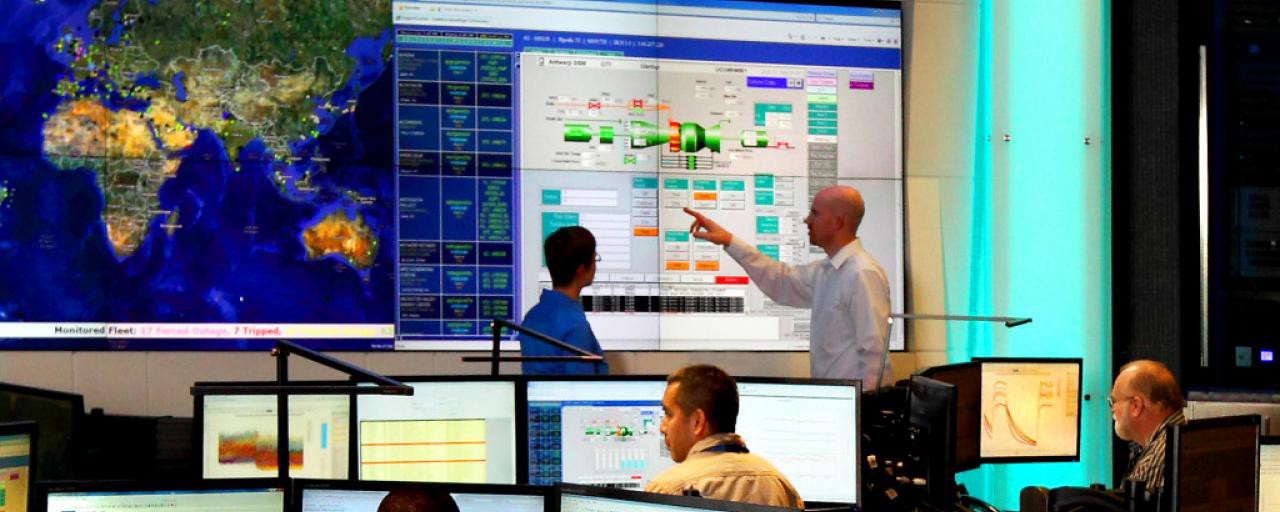
Changing the economics
We’re fortunate to be in front of two major technology trends in the industry. First, decreasing sensor and communication costs has resulted in exponential equipment data growth. Detailed instrumentation data is no longer limited to multi-million dollar assets. Cars today generate gigabytes of data per day. Even electric meters and thermostats can capture diagnostic data. This data is more readily accessible, whether via cellular networks or new radio networks designed for low power communications (NB-IOT, LoRa, etc.).
Second, cloud-based infrastructure allows for inexpensive storage and compute for all this new sensor data. The fixed costs of existing solutions from the large manufacturers can be distributed over a large install base, with equipment from multiple manufacturers.
All this means that the data capture, communication, and visualization can be done economically for most new equipment. What about the analytical expertise of the manufacturer and end-user engineers?
My co-founder, Will Vega-Brown and I were classmates at MIT. He went on to do his PhD at MIT’s Computer Science and Artificial Intelligence Laboratory (CSAIL) while I worked at GE and then completed my MBA at Harvard. Will developed new machine learning methods for planning and optimization. He realized that these methods and related advances in survival modeling could be applied to industrial equipment. These new methods can effectively augment human engineers, increasing their productivity by allowing a single subject matter expert to monitor thousands of assets continually.
By combining newly available equipment data and our advances in machine learning, we can effectively estimate the remaining life of an asset. These estimates update continually as we receive new data, providing engineers with an empirically-driven understanding of equipment health.
Step 1: Universal asset data management
Our first step has been to build a platform capable of managing diverse industrial equipment data. This includes, metadata, such as the manufacturer and date of installation, time series data, including sensor measurements and manually collected measurements, and unstructured data such as maintenance logs and equipment photos.
With a platform consolidating all this data, we have replicated many of the capabilities of leading remote monitoring centers. By delivering our platform as a web application, we enable users to access real-time equipment data from anywhere they have Internet access.
The first iteration of our platform, codenamed Asgard, is deployed now with our beta customers and partners.
Step 2: A new breed of predictive analytics
Machine learning has advanced dramatically in certain fields, beating the best human players at Go, exceeding humans in image recognition, and in recommending your next online purchase. All these examples have an important prerequisite: a very large amount of training data. Facebook, for example, collects over two billion new photos per day. All these examples help new machine learning models to become extraordinarily accurate.
Fortunately, we don’t see two billion equipment failures per day. Unfortunately, this means there isn’t nearly as much training data for predicting equipment failure as exists for more common machine learning application. We mitigate the issue by focusing on very specific equipment types: to start, certain classes of transformers and membrane-based water processes. Additionally, we are fortunate to work with some of the largest equipment operators in the world, allowing us to have already integrated tens of thousands of assets and thousands of failure examples.
All this data allows us to reliably estimate the time until an asset fails, the probability that it fails in a given period, and to benchmark the performance of an asset against a larger fleet. With more data still, we can diagnose equipment issues before they are apparent to operators. Our platform does this 24/7, for assets around the world.
Inventing the future
We’ve based our company in Somerville, Massachusetts, to be close to our roots at MIT and to take advantage of the strong tech community in Boston. We are also proud members of Greentown Labs, the largest clean energy accelerator in the US.
We as a team are excited to democratize advanced equipment monitoring and prognostics. We believe our technology will reduce unplanned equipment downtime, defer equipment replacement, and increase operator safety at an unprecedented scale.
For more information, please send us a note at hello@tagup.io, or visit our website.